Long-haul delivery optimization and logistics management automation
Introduction
Long-haul delivery demands accurate planning as much as last mile delivery. Heavy-duty vehicles spend lots of hours loading and unloading. Therefore, mistakes made when scheduling deliveries may increase downtime and, consequently, transportation costs. At the same time, fast and high-quality routing can bring significant savings to a company.
Below, we will tell you about our joint project with a logistics company. Read this case study to learn what solution we have developed for long-haul transportation management and what benefits it has brought our client.
Client profile
Description:
A logistics company that provides long-haul transportation services to businesses.
Fleet:
2,700+
vehicles
Workforce:
3,000+
employees
Pool of drivers:
2,300+
drivers
The company performs delivery throughout Europe and Asia over a total area of over 5800 thousand mi². Its bases are located in large cities with a population of over 1 million people. The company’s fleet includes over 1,300 tractor-trailers and 1,400 semi-trailers of various types.
Problem
In 2021, the company's management decided to implement an optimization tool for transportation planning and logistics management. This idea came up while studying the successful cases of last mile delivery optimization. The company's experts suggested that the solutions they explored could be adapted for the current tasks and effectively used in everyday operations afterward.
Trip scheduling, which performed well in last mile delivery, looked promising for long-haul freight, which involves changing tractor-trailers during the transportation of semi-trailers, and where the "maneuvering" and maintenance of loading and unloading operations at customers’ warehouses are carried out by a separate fleet of tractor-trailers.
Although the last mile delivery has become the most sensitive link in the supply chain, large- capacity transportation scheduling also plays a significant role in developing an efficient system. This is particularly the case for transportation, where distances of more than 700 miles per day are involved, and the level of service is measured in minutes.
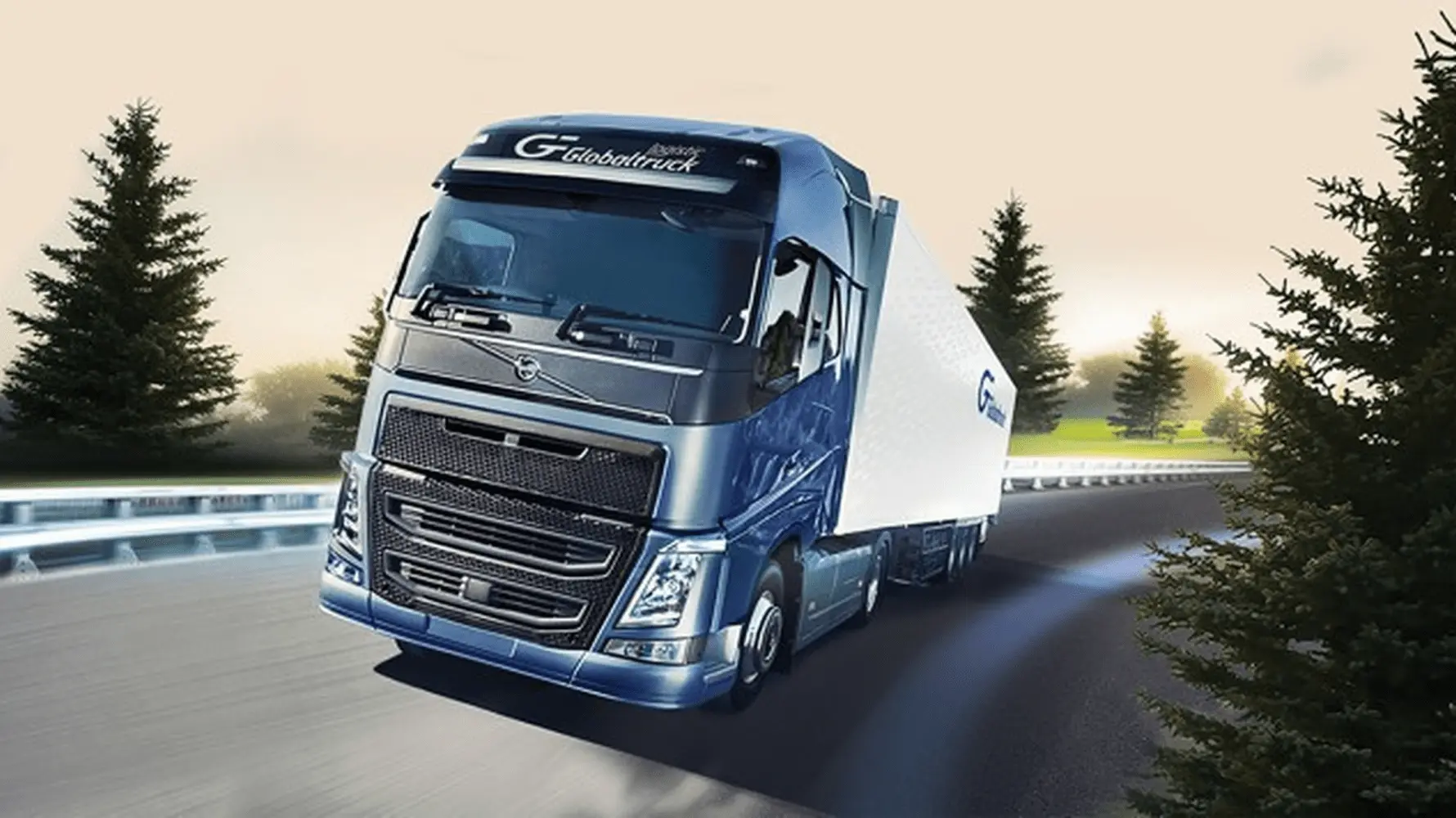
At certain stages in the company's life, daily logistics operations can be successfully performed by hand, but as the business scales, manual planning becomes a bottleneck and generates inevitable problems:
Influence of the human factor
The logisticians who distribute orders between the vehicles and plan their routes are struggling with huge operational workloads. They have to constantly monitor each car's location, promptly adjust the schedule, and inform the client about current changes. At the same time, both downtime and vehicle shortages should be avoided. The need to operate with a large amount of data prevents an employee from making optimal decisions and increases the risk of mistakes.
Reduction of the vehicle utilization
Heavy vehicles spend hours at the points of loading and unloading. Therefore, errors in scheduling not only decrease the client service quality but also raise the vehicles' downtime. Consequently, this increases transportation costs.
The optimizer was implemented to improve logistics efficiency as well as to eliminate such vulnerabilities in the transportation system.
Previous to cooperation with Veeroute, the company attempted to create its own solution for automating logisticians’ work. The developed prototype was capable of eliminating high-level errors, but it did not take into account the entire amount of input data needed for optimal planning. The program could not consider the route convenience and geolocation; moreover, it did not have enough power to carry out complex mathematical calculations. At the same time, the prototype did not have a user interface.
After analyzing the prototype’s effectiveness, the company's team abandoned their own solution's development in favor of collaboration with a technology partner.
In the summer of 2021, the company decided to launch a joint project with Veeroute and HomeStretch.
HomeStretch - a software company developing SaaS for scheduling routes and tracking their execution. Veeroute's partner.
Challenge
At the beginning of the project, two main goals were established:
Automate and standardize the work of logisticians.
Increase the efficiency of logistics operations by optimizing the routing and distribution of vehicles according to clients' requests.
Considering the previous experience of the company, the primary terms of reference were determined. Within them, these key metrics were identified:
- increase in productivity per car, expressed in the number of operations. A KPI of 1.6 was set, which expresses the number of customers' requests served by 1 tractor-trailer per day.
- mileage savings. The KPI was not set because as long as the project was being piloted, no significant numerical changes were expected.
Additionally, another task was formulated: to reduce the mileage on toll roads. However, by the nd of 2021, it was solved by organizational means — without using technical resources.
Solution
The project started in the summer of 2021.
The HomeStretch team took over the creation and integration of the user interface. The Veeroute optimizer became the mathematical core of the solution.
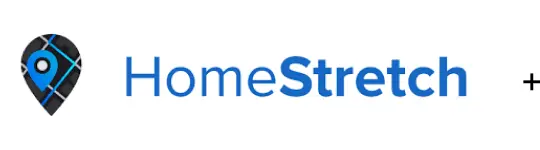
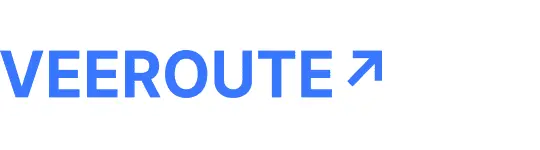
The first step was to prepare the initial terms of reference, in which, in addition to the main performance metrics, the company's logistics model was described.
The logistics model of the company
The company provides the customer with semi-trailers. After the client loads them with goods, the semi-trailers return to the company's base.
The company drives semi-trailers from one city to another between its own bases.
Semi-trailers are transported from the company's base to customers, unloaded, and returned to be sent on a new trip.
One of the key features of this model is the existence of two separate entities: a tractor-trailer and a semi-trailer. Each entity has its own logic, and this had to be considered when developing the solution.
In order to improve the efficiency of the current logistics model, two primary areas of work were identified:
Optimization of the vehicles' operation in cities — that is, the delivery of semi-trailers between the bases and customers' warehouses.
Automation of order distribution between the semi-trailers.
Stages of the project
In the summer and fall of 2021, the Veeroute team was engaged in creating new entities for the system and fine-tuning the optimization engine, considering the features and requirements of the client.
In November and December 2021, theoretical calculations were made. The team carried out transportation planning and business logic testing in parallel.
At the beginning of 2022, the pilot project was successfully finished. After reviewing it's results, the company's management approved the start of integration.
In March and April 2022, the HomeStretch team carried out the integration. The directories were purified since incorrect data could affect the work of the optimizer.
In May 2022, the product was fully prepared to work on real data.
Since June 2022, the solution has been actively used in the company's operations.
Results
After a month of work with the optimizer, the company's team summed up the first results and noted an explicit positive effect.
The KPI was successfully met.
Transport productivity, expressed in the daily number of orders per car, increased by 8% in the first month of using the solution.
Savings on mileage amounted to 12%.
According to the company's experts, due to the saving on mileage, the optimizer began to pay for itself within the first month of work.
Route planning time was reduced from 4-5 hours to 15 minutes.
Reducing the calculation time by 95% allowed the company to achieve a more stable level of service. It’s critical during seasonal periods of high demand for heavy transportation, during which the entire operational staff’s workload will increase significantly.
All the key elements of the company's business logic were successfully met by the user interface features developed by HomeStretch. Automating the work of logisticians and lowering the volume of monotonous work made it possible to reduce the number of operational errors.
The heavy transportation market has always been and remains highly competitive due to the low entry threshold. A slight difference of a few percent in costs and level of service separates successful companies from those who have to face bankruptcy. We are committed to building the most reliable and efficient business model in our industry. As long as this goal requires adaptation and implementation of digital solutions, even from related logistics sectors, we are always open to new ideas. I consider the experience of cooperation with HomeStretch and Veeroute to be very successful. The project showed profitability from the first month of its operation.
Development and Logistics Director