Routing automation and express delivery optimization for a pharmacy chain
Introduction
The rapid growth of online sales is often associated with an extreme load on the logistics system. Planning routes, distributing orders, recruiting new couriers—all this begins to require more time and more resources. In this case, automation can be a convenient solution: it will help reduce the amount of operational work and make business scaling more comfortable.
In this case study, we are going into detail about the problems that automated routing can solve and how delivery optimization is related to social justice.
Client Profile
A large online service for the sale and delivery of medicine and goods for beauty and health.
10 000+
pickup
points
50 000+
product
range
3 000+
employees
in 70+ cities
The company was established in 2011. In 2020, it launched a mobile app for ordering drugs. About 300,000 people from over 70 cities across Europe and Asia use it every day.
Situation
In 2020, after the COVID-19 pandemic and subsequent self-isolation began, the number of online purchases in all retail segments increased sharply. The pharma industry was in for truly explosive growth. According to Admitad, in the first quarter of 2020, the number of online sales of drugs, medical supplies, and related services increased by 46% compared to the previous year's results.
The company's turnover grew by 96% in 2020, and it successfully adapted to the new operating conditions. However, as a result of intensive scaling, the company had to face a new challenge: as the volume of orders grew, the load on logistics increased significantly. At the same time, the company's delivery model began to develop quickly.
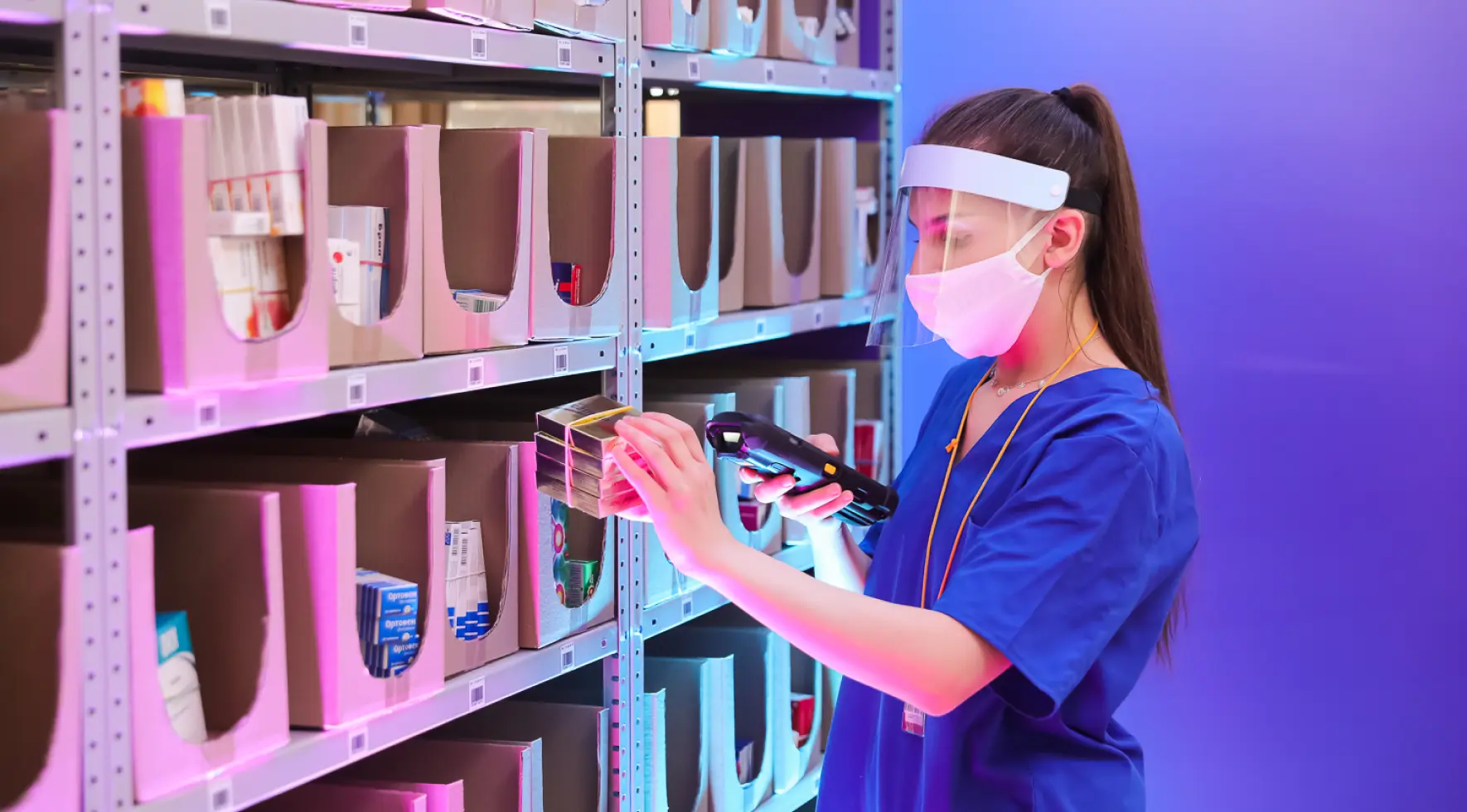
Problem
At the end of 2020, the company's employees processed and delivered at least 20-40 thousand orders per day throughout the largest delivery region. As the sales volume increased, it became more difficult and time-consuming to plan the delivery manually, and the couriers’ working time was used less effectively. That could lead to an increase in time spent and transportation costs.
Let's analyze why.
1. Exclusive role of a logistician.
In addition to pickup points in drugstores, the company's logistics model involves large warehouses—hubs, whose areas vary from 4,300 to 10,800 square feet. Every day, several dozen logisticians were planning deliveries from hubs in the ERP-system.
There were bottlenecks in their operation scheme:
- Logisticians could only serve hubs in their residential cities, as it was only in those zones that they were well acquainted with the details of transport logistics.
- Only a logistician could perform the routing. Other employees did not have the appropriate skills or access to the ERP-system.
During the working day, the logistician needs to plan routes for several waves of delivery. Each of them is tied to the delivery interval chosen by the customers. The wave duration varies from 3 hours or more, depending on the city.
To be sure couriers are able to deliver orders on time, the logistician must do these steps an hour before each interval begins:
Do the routing and make a delivery plan
Instruct warehouse staff
Make sure that orders are collected and issued to couriers
Solve problems with orders that arise while planning and transfer them to the contact center to communicate with the customers
If the logistician spends too much time on routing, the couriers may not have enough time to receive orders before the interval starts. At that point, it turned out that route planning in a particular city was the exclusive responsibility of a particular logistician. All processes on the last mile depend on that person, and no one could replace them or share their tasks.
Until 2020, logisticians successfully tackled manual delivery scheduling for each wave. However, when the volume of orders increased to 300-500 orders per wave, routing became more and more time consuming and less effective. By the end of 2020, routing could take up to half an hour for a wave. This situation created risks for fulfilling the SLA. This was concerning, as the high level of service is an important competitive advantage of the company: the couriers deliver at least 95% of orders on time.
Non-optimal utilization of couriers.
The sharp increase in the sales volume led to the need for a large number of couriers. It was fairly difficult to find and train them in a short timeline, and moreover—if couriers are not satisfied by the number of orders and the payment, then they will leave.
In order to solve the staff turnover problem, the company implemented the principle of social justice. All couriers had to receive the same amount of money for 2 weeks, as it is the standard salary payment period. This principle had to be considered when distributing orders so that all couriers would receive approximately the same amount of work.
Since only the logistician was involved in route planning and distribution of orders, it depended specifically on the logistician how much money the couriers received in piecework payment.
Considering that logisticians were forced to work in conditions of high workload and severe time constraints, the human factor could intervene in the distribution of orders between couriers. For example, a logistician could randomly assign more orders to one courier than the other. The lack of transparency threatened the principle of social justice.
Also, the company had a staff of couriers on an hourly basis, for which different tariffs could apply. During the working day, if each of the couriers received fewer orders than they could fulfill, this would lead to downtime and increased costs. Logisticians had neither the time nor the opportunity to manually analyze and optimize the cost of couriers' salaries—and this was compounded since the number of couriers was constantly growing.
Various types of goods.
Among other things, it is worth noting that the wide variety of goods became an additional factor in the complexity of planning delivery.
Drugs and medical supplies are goods that differ not only in consumer properties but also in the transportation method. Within the same order, there may be items that can be transported in the usual way alongside items that must be refrigerated. The latter include heat-labile drugs—for example, enzyme dragees and solutions for injections.
All these features (and many more) must be kept in mind while route planning in order to optimally distribute the current orders between couriers.
The company's catalog contains more than 50,000 items, each of which has a certain set of significant characteristics. In the aggregate, this is a huge amount of data that is physically impossible for an ordinary person to navigate efficiently.
Search for an optimization partner
In Fall 2020, the company's management decided to develop its own platform for automating and optimizing logistics and started its search for a technology partner.
The future solution was supposed to combine automated logistics management and fast efficient routing. Also, the product needed a user-friendly interface with a mobile app for couriers, which would display current data for each trip in real time, including refunds, cancellations, combined orders, etc.
Important criteria during the partner selection process were:
Optimization speed and quality
The ability to consider business logic details while routing, including time windows, different types of goods, postponed deliveries, returned orders, etc.
The ability to make improvements to the product
Easy integration
10 different contenders were considered by the client. Most of them could only offer a ready-made boxed solution that did not allow for further improvement of the product according to the customer's requirements. Other solutions also did not meet all the stated criteria.
In 2021, the company's team decided to partner with Veeroute.
Challenge
At the beginning of the collaboration, the company's team set two goals to reach in cooperation with Veeroute:
Make the route planning process easier and faster
Optimize the operation of couriers and increase their load
The route planning time for one wave of 300-500 orders was set as a main KPI. Before the project launched, the routing time took about 20-30 minutes. The goal was to cut the time by half, so the KPI amounted to 10 minutes.
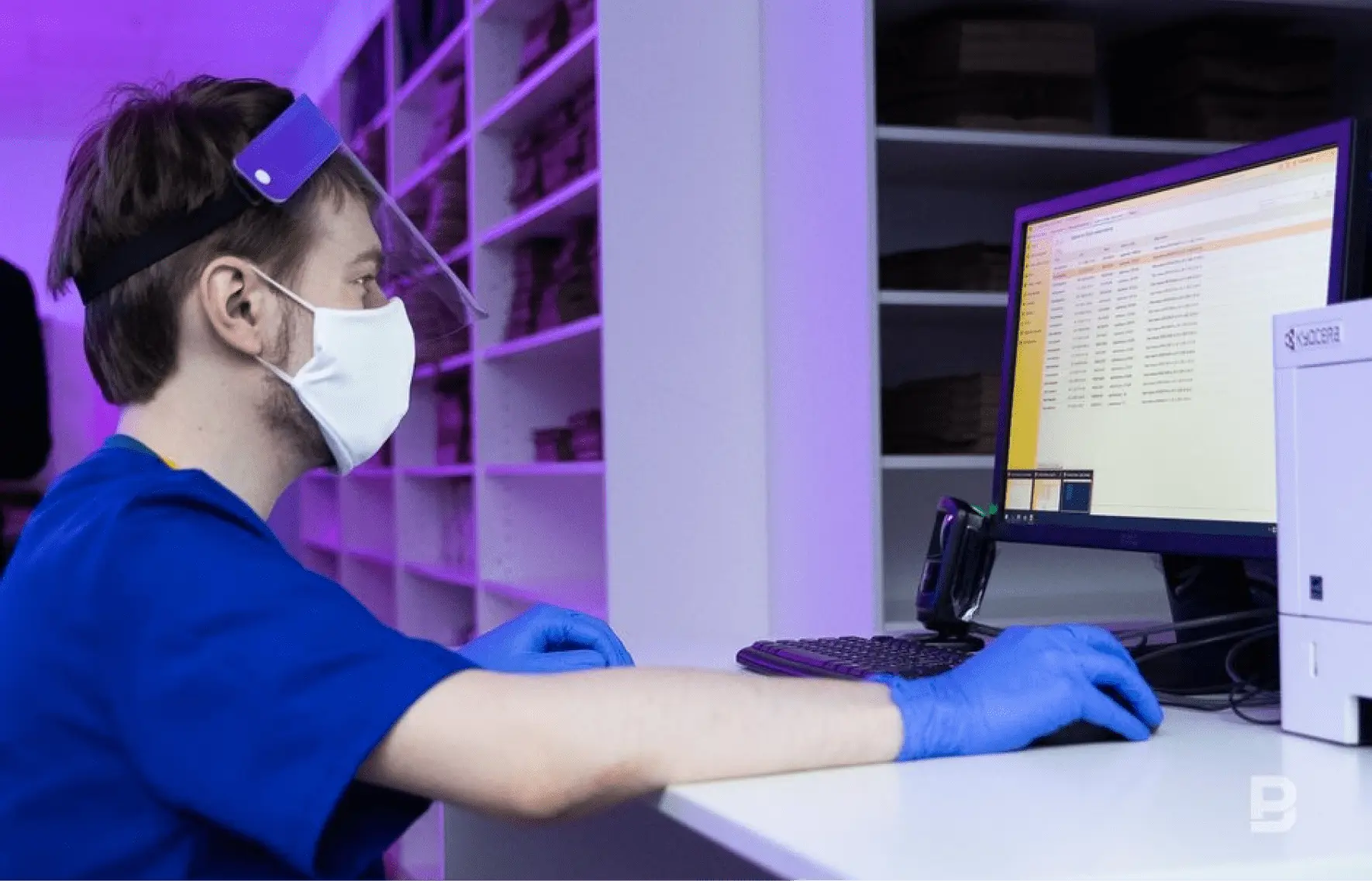
Solution
The collaboration began at the end of 2020. In September 2021, a pilot project was launched to optimize delivery in a test city, a megalopolis in the south of the whole delivery region. This city with a population of over 1 million people has complex logistics, high population density, traffic jams, and a large number of orders.
Using the example of a city with compound infrastructure, the joint team could see how the optimizer copes with a wide variety of real-world tasks and analyze its work.
In Fall 2021, the company's team collected feedback based on the results of the pilot project. After careful data processing, the launch was considered successful, and in Fall 2022, the project’s geography was expanded to all the cities of the company’s presence.
Results
In December 2022, the company's team shared the first results of Veeroute’s operation and their observations:
Routing has become vastly easier.
Automated routing made it possible to significantly simplify the technical aspect of delivery planning and eliminate the bottlenecks:
- Before Veeroute's implementation, only a logistician could perform the routing. Now this task can be delegated to another employee, whether it be an operator or a warehouse worker. The software only needs to be set up once; after that, it only takes a few keystrokes to schedule a delivery.
- Since detailed information about different cities is already loaded into the system and considered when optimizing routes, a single logistician can serve several cities at once.
Route planning time was reduced by 50%.
At the end of 2020, routing took about 20-30 minutes for a wave of 300-500 orders. Now it takes no more than 10-15 minutes, depending on the region and delivery volume.
Utilization of couriers increased by 18%.
During the project, the problem of couriers’ high workloads was solved by organizational means. However, optimization and automated routing helped accelerate the achievement of results: the average number of orders per courier increased from 27 to 32 per day.
Due to automation, the distribution of orders between couriers has become more transparent. Since the plan is formed by the system, the salary level of employees is no longer influenced by the human factor, which allows the principle of social justice to be maintained.
Transportation costs have been reduced by 10-15%.
Routing optimization helped achieve a more efficient distribution of resources and working time of employees. Thus, the company managed to reduce the cost of courier delivery by 15%.
Future plans
Because the solution succeeded and showcased excellent results throughout the delivery area, the company plans to fully automate business processes in the last mile delivery.
Specifically, the company plans to decouple the courier's work schedule from waves and introduce a self-pickup system. In the future, when a courier arrives at the hub at a specified time, they will be able to independently pick up an order and immediately start delivery. The order is prepared by warehouse employees, and the courier just has to use the number from the mobile app to retrieve it from the shelf. This will help reduce courier downtime, optimize the work time of warehouse workers, and further reduce delivery costs.
Automation is the foundation for business scaling. Thanks to Veeroute’s optimization, we were able to improve the efficiency of business processes and create a basis for the further development of logistics. Automatic routing has reduced the operational load and freed up resources for other tasks.
Technical Director of Logistics